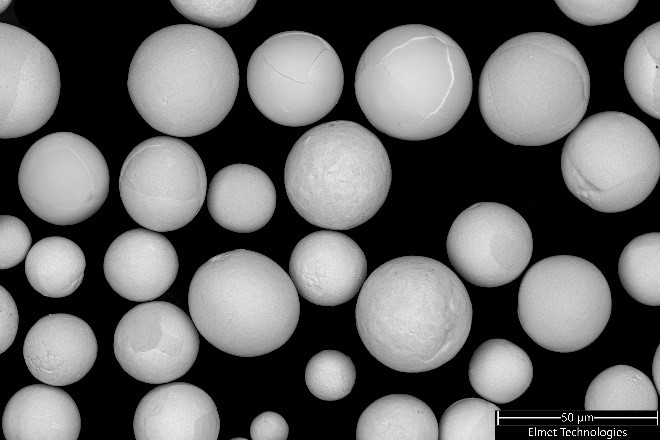
Pure Molybdenum AM Powders
Elmet Technologies is a global leader in pure molybdenum AM powder production, delivering premium-quality materials for laser-powder bed fusion additive manufacturing processes. We meticulously craft our molybdenum powder to deliver exceptional high-temperature strength, outstanding corrosion resistance, a low thermal expansion coefficient, and superior thermal conductivity. We ensure low oxygen content, excellent flowability, and high apparent and tap densities, making our molybdenum powder a versatile material trusted across numerous industries and applications.
Our pure molybdenum AM powder shares many characteristics with pure tungsten but excels with its significantly lower density—just half that of tungsten—making it an optimal choice for lightweight applications that demand uncompromising strength and durability. At Elmet, we ensure precision in every process, producing molybdenum and molybdenum alloy powders with tightly controlled particle size distributions, targeting a mean particle size range of 3-30 µm.
Pure MOlybdenum Am POwder Chemical Characteristics
Element | Percent% |
Mo | 99.9 min |
C | < 0.01 |
O | < 0.03 |
Pure MOlybdenum AM Powder Physical Characteristics
Property | L-PBF | DED |
Bulk density, g/cc | > 5.2 | > 5.2 |
Flow, s/50g | < 12 | < 14 |
PSD, d10, µm | > 10 | > 40 |
PSD, d90, µm | < 53 | < 150 |
Tailored Molybdenum Solutions for Advanced Engineering
Additive manufacturing and powder metallurgy rely on advanced techniques like isostatic pressing and metal injection molding to create high-performance components. Elmet Technologies specializes in premium molybdenum and molybdenum alloy powders tailored for these applications.
Our powders, with controlled particle sizes from 3 to 30 microns, meet the precision demands of AM. Their custom-engineered properties ensure consistent performance in challenging environments.
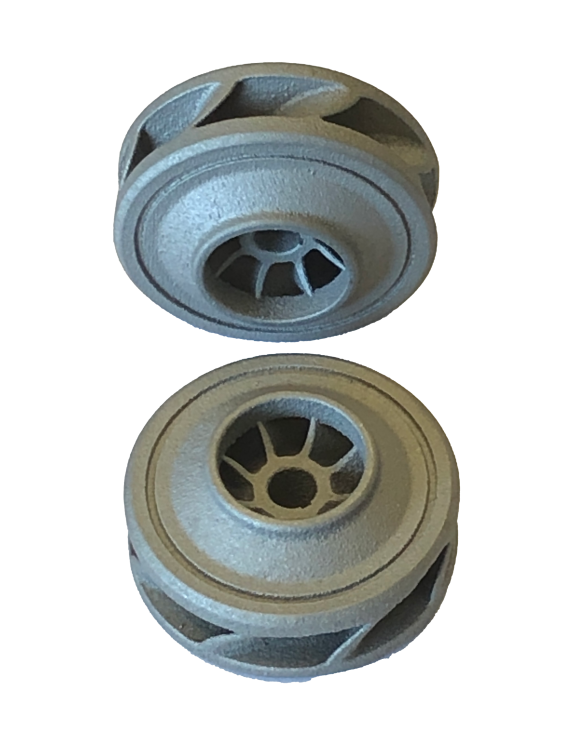
MO Powder Production
Spray Dry & Plasma Densification
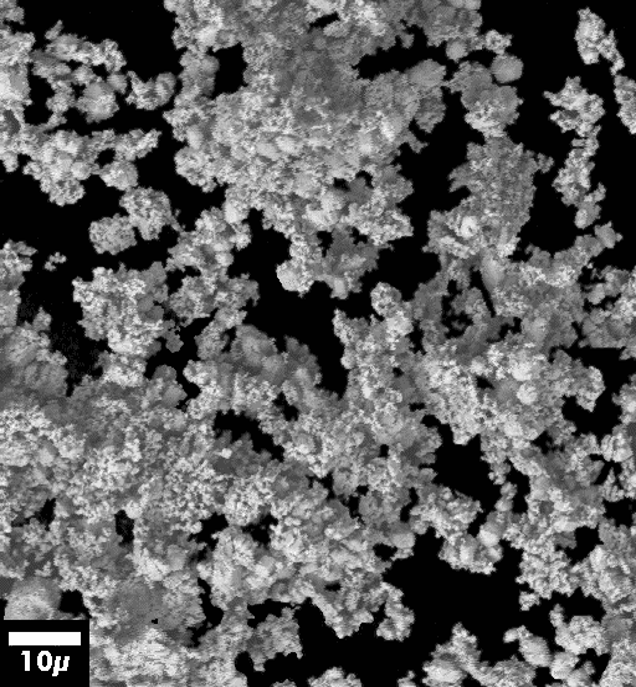
Incoming Mo powder
Mo feedstock
no flow
1 – 50µm size,
1.2 g/cc density
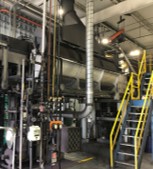
Spray Dry Process
Spray drying atomizes and dries slurry to spheres.
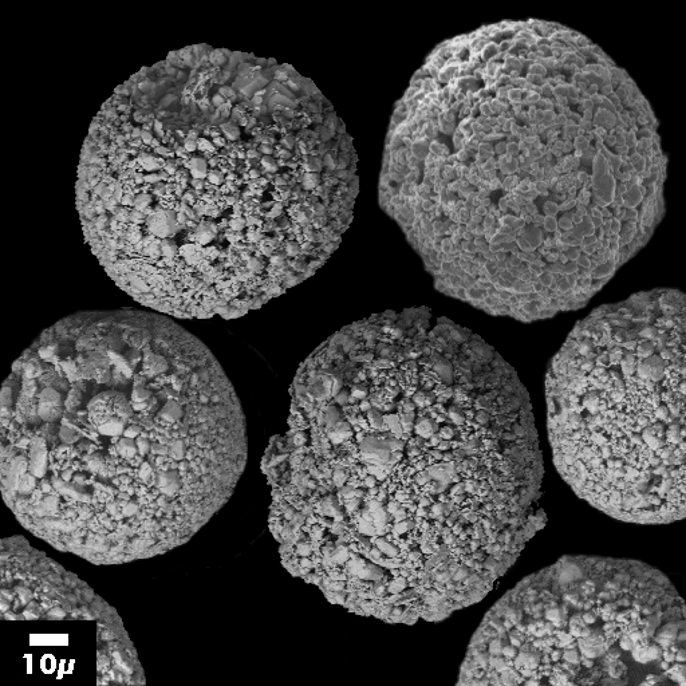
Spray Dry Powder
Spheres
25 s/50g flow
20 – 100µm size
2.5g/cc density
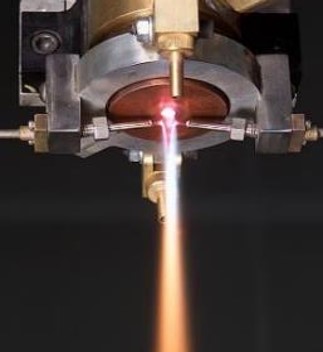
Plasma Process
Melts spray dried powder in 20,000° flame
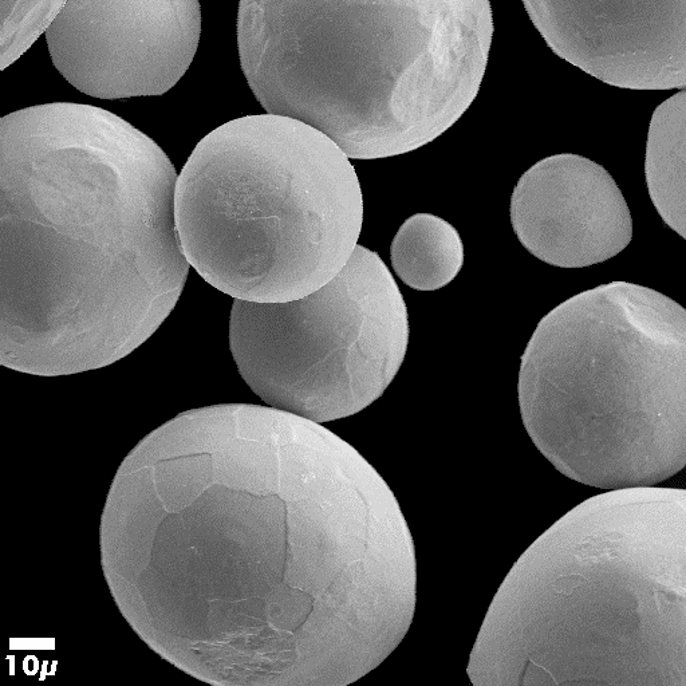
Plasma Densified Powder
Fully dense spheres
10 s/50g flow
10 – 100µm size
>5g/cc density
High-Performance Molybdenum Products
- Sheet: Elmet offers a variety of cold-rolled sheets in different thicknesses and lengths, starting from metal powder, pressed into ingots, sintered, and rolled.
- Foil: We provide foil in standard thicknesses from .001″ to .005″ (and thicker), customizable in size, thickness, length, surface finish, and other properties.
- Plate: Elmet supplies high-quality molybdenum and tungsten plates in standard thicknesses, customizable in size, thickness, length, and surface finish.
- Rod: We manufacture and stock common sizes of tungsten rods for various applications, including semiconductors, lighting, and high-reliability diodes.
- Wire: Elmet produces and stocks molybdenum, molybdenum potassium-doped HCT, and tungsten wires, with sizes as small as 0.0007″.
- Precision Machined Components: With decades of expertise, Elmet utilizes over 70 advanced machines to deliver superior tungsten and molybdenum machining and fabrication solutions.
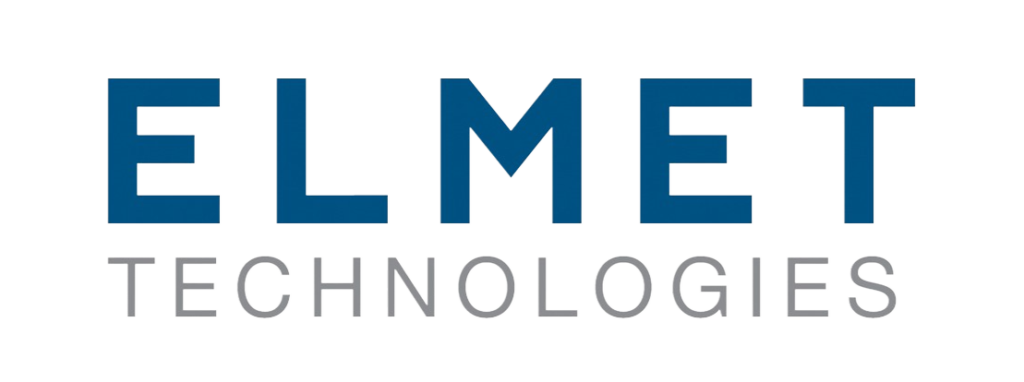
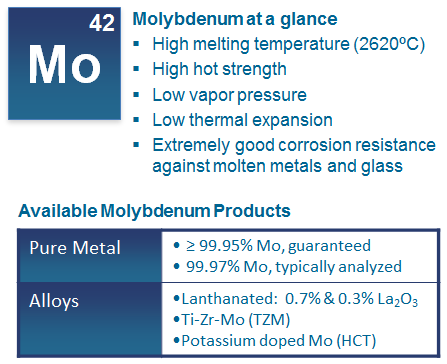
Pure Molybdenum Powders for AM
Powder Grades | Bulk Density (g/cc) | Hall Flow Rate (s/50g) | Particle Size D10 (mm) | Particle Size D50 (mm) | Particle Size D90 (mm) |
PDMP – L-PBF (10 – 50 µm) | > 5 | < 15 | > 10 | 25 -35 | < 50 |
PDMP – DED (40 – 150 µm) | > 5 | < 17 | > 40 | 65- 75 | < 150 |
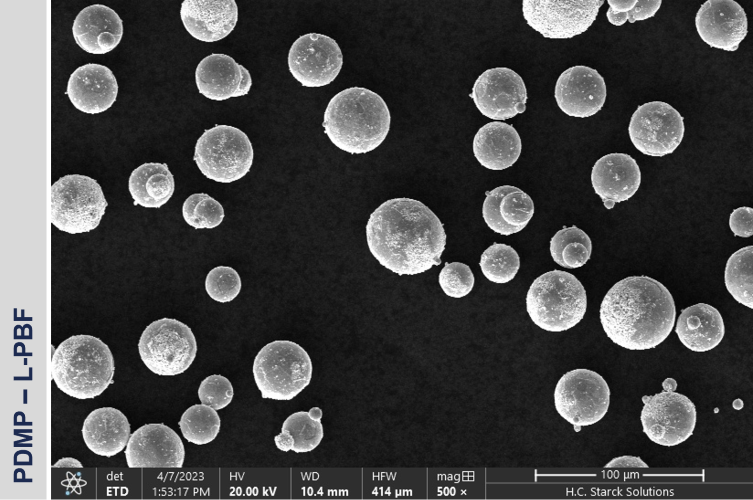

Mo Material Facts & Figures
- Symbol: Mo
- Category: Transition Metal, Group VI
- Atomic Number: 42
- Density: 10.28 g/cm³
- Discovered: 1778
- Melting Point: 2620 °C
- Load Bearing: Up to 1600 °C
- Thermal & Electrical Conductivity: Excellent
- Low Vapor Pressure: At high temperatures
- Thermal Expansion: Minimal coefficient
- Corrosion Resistance: Exceptional
- High Energy Shielding: Effective protection
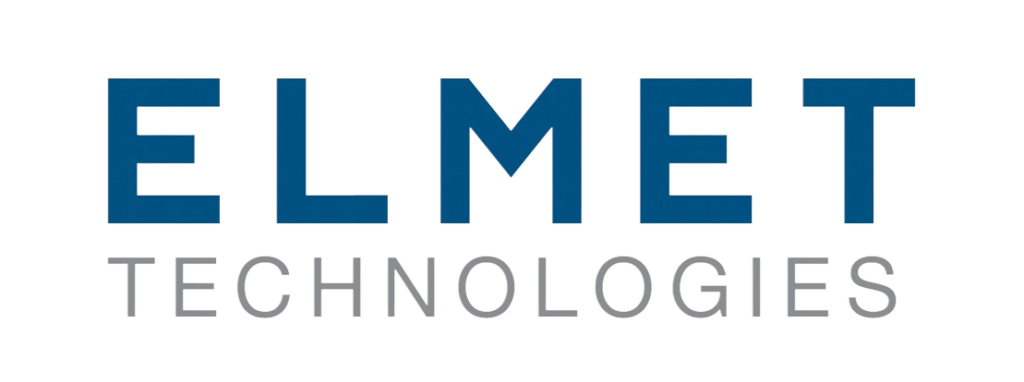
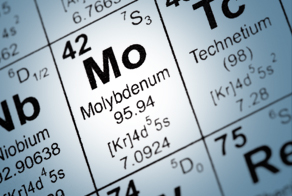
Benefits of Additive Manufacturing With Molybdenum
Additive manufacturing is ideal for producing intricate molybdenum components, meeting the growing demand for complex geometries across industries. Molybdenum powder is perfect for this process due to its unique properties: excellent alloying capabilities, high flowability for smooth 3D printing, a high melting point for heat resistance, and versatility across techniques like Laser-Powder Bed Fusion (L-PBF) and Directed Energy Deposition (DED). It enables the creation of precise, high-performance parts efficiently.