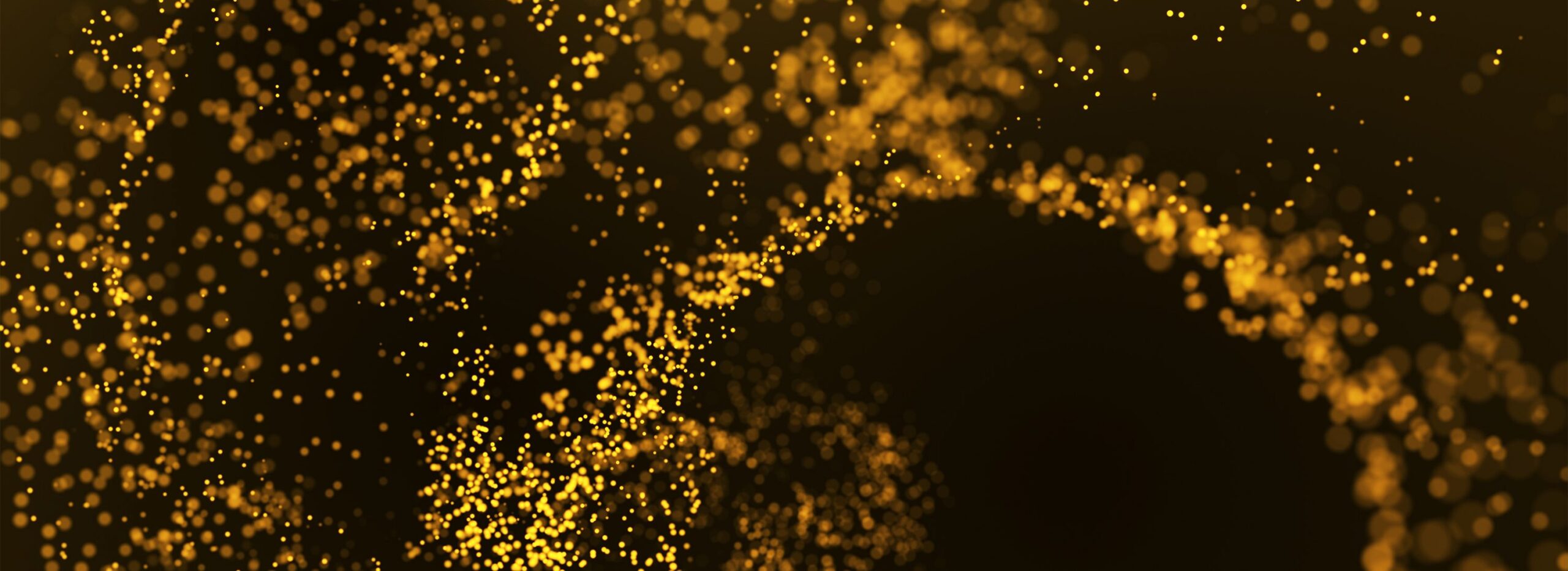
Additive Manufacturing Refractory Metal Powders
Elmet Technologies is a global leader in high-quality refractory metal powders, driving advancements in additive manufacturing (AM). Our innovative AM powders are essential for rapid prototyping and the creation of complex, high-performance engineering components. The versatility of these powders allows us to fabricate intricately designed parts that are difficult to produce using traditional manufacturing methods.
Moreover, they offer a cost-effective solution for low-volume production while significantly enhancing material utilization, particularly in costly materials. As the technology surrounding AM powders continues to advance, the scope of their applications expands, leading to innovative uses in fields such as biomedical, propulsion, and heat management systems.
Powder Processing
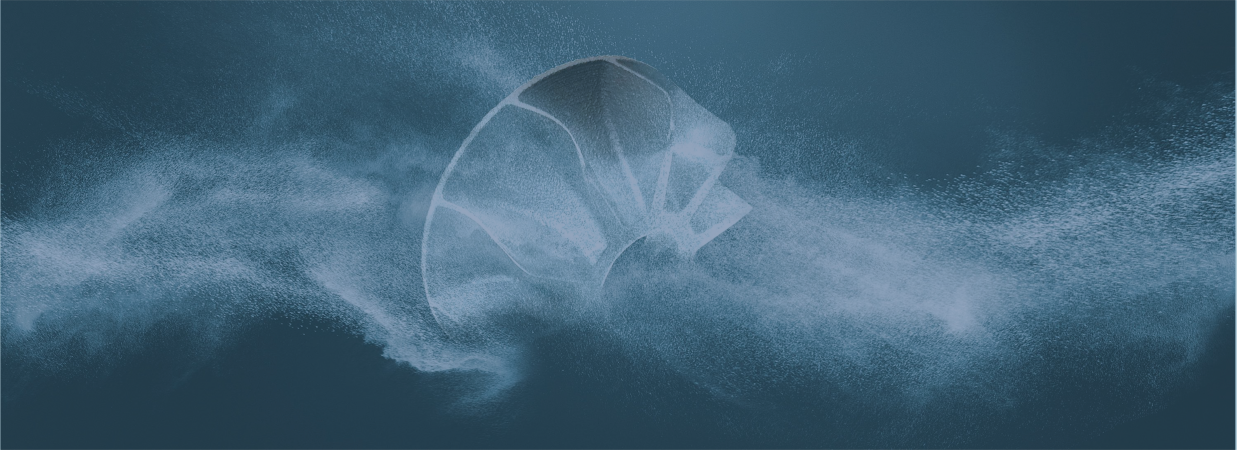
Our Customized Additive Alloy Powders Product Portfolio
Tantalum Alloys
Ta-2.5W, Ta-5W, Ta-7.5W, Ta-10W
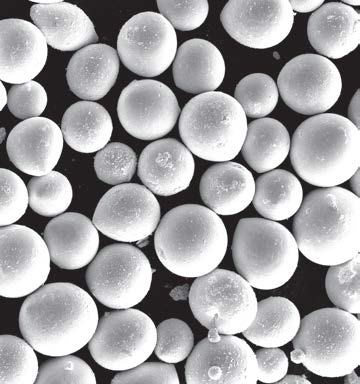
We continuously develop new materials and methods and are ready to support your unique requests.
MO Powder Production
Spray Dry & Plasma Densification
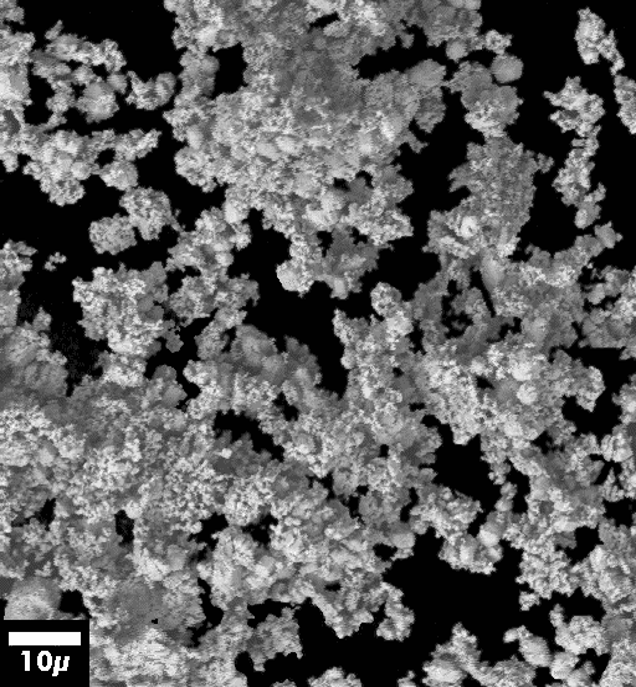
Incoming Mo powder
Mo feedstock
no flow
1 – 50µm size,
1.2 g/cc density
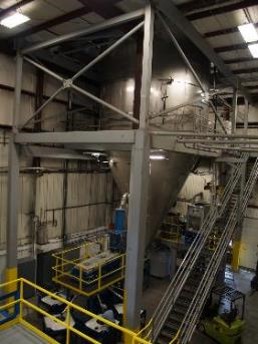
Spray Dry Process
Spray drying atomizes and dries slurry to spheres.
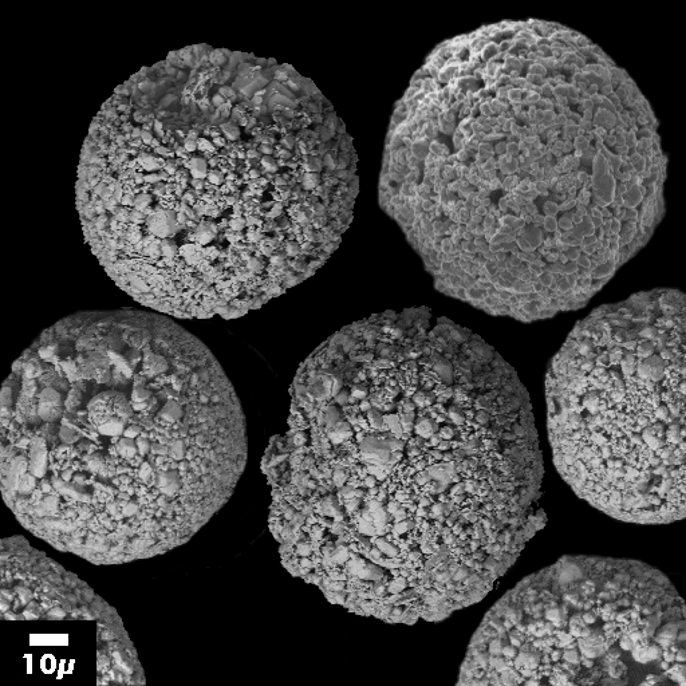
Spray Dry Powder
Spheres
25 s/50g flow
20 – 100µm size
2.5g/cc density
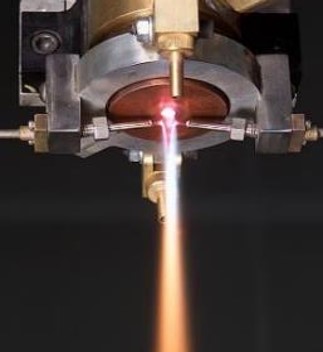
Plasma Process
Melts spray dried powder in 20,000° flame
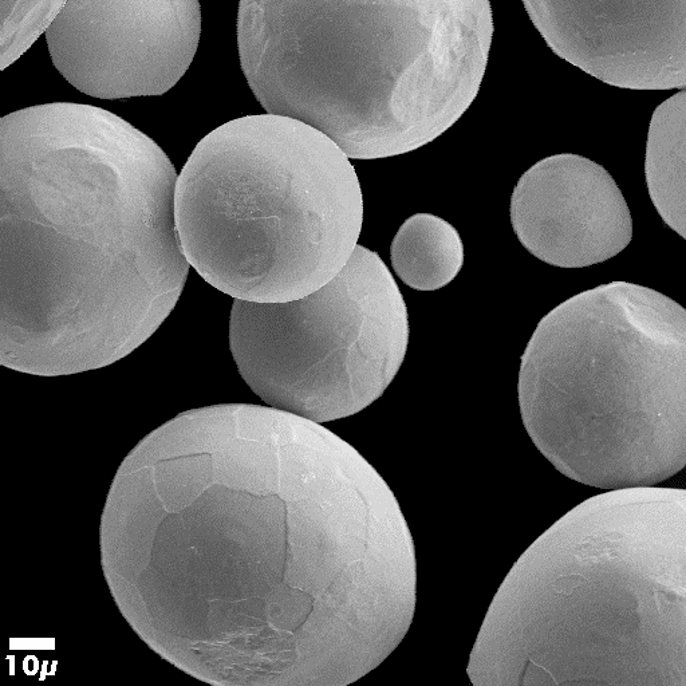
Plasma Densified Powder
Fully dense spheres
10 s/50g flow
10 – 100µm size
>5g/cc density
Powder Production Non-Reactive
Spray Dry / Plasma Densification
- Class 1,2,3 typically produced
- Mo and alloys, W and alloys
- TZM, MoLa, MoRe (10,41,48Re), MoHfC, MoReHfC
- WRe (1,3,5,7,24, Re)
- Tungsten Heavy Alloy
Powder Production Reactive
Electrode Induction – Melting Gas Atomization (EIGA)
- Uses melted ingots, extruded, and machined bars as feedstock
- High yield, low oxygen powder produced
- Reactive metals – Ta, Nb, Nb-C103, Cb-752, FS-85
- L-PBF (-50 + 15µm) and DED (-150 + 40µm)
Applications Provided
Laser – Powder Bed Fusion (L-PBF -50 + 10µm)
Laser – Powder Bed Fusion is an advanced additive manufacturing technique where layers of spherical metal powders are spread and fused with a laser, resulting in precise and smooth parts. Elmet Technologies customizes powders to ensure high-density, high-quality outcomes for diverse applications.
- Production-ready and R&D materials: W, WHA, WRe, Ta W, Mo, MoRe, Re, TZM, Nb, C103, Ta, Ta-5W
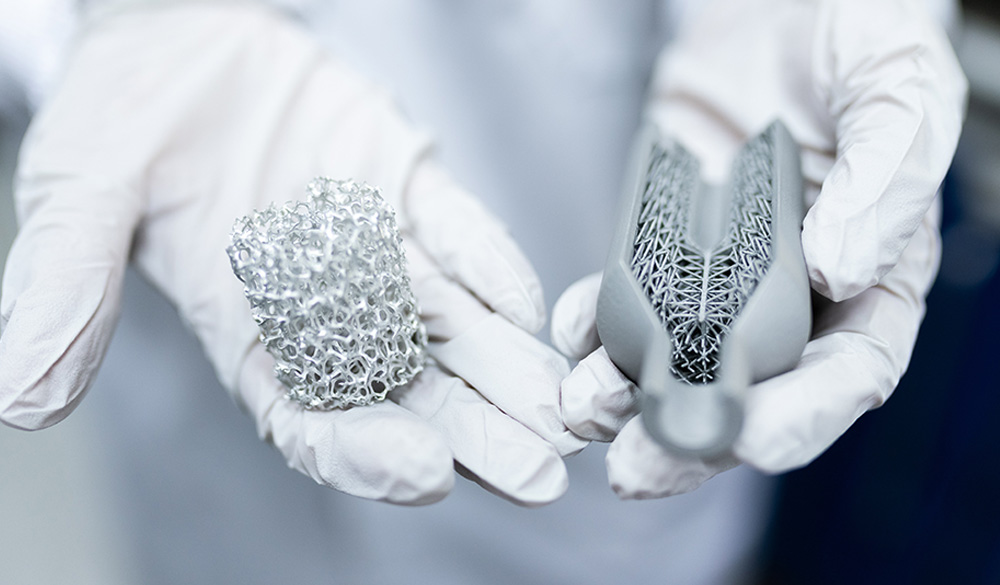
Additive Manufacturing Materials
Our powder feedstock boasts tailored properties perfectly suited for the additive manufacturing industry. Our core competencies in tungsten (W), molybdenum (Mo), tantalum (Ta), and niobium (Nb)—in both pure and alloyed forms—ensure that our customers receive only the highest quality materials.
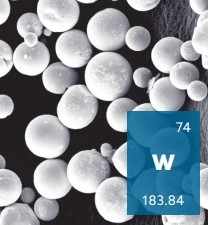
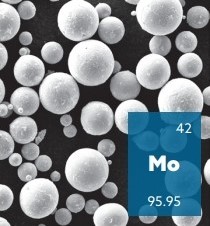
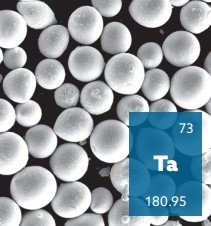
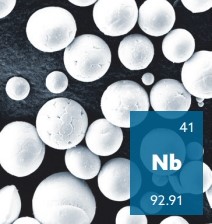
High Performance Refractory Metal Material
Our advanced manufacturing technology, integrated supply chain, and metallurgical expertise combine to produce high-quality refractory metal feedstocks precisely tailored to your needs. These feedstocks deliver exceptional material properties and optimal performance, meeting the rigorous demands of additive manufacturing applications.
Their properties exceed traditional production specifications and offer:
- High purity
- High bulk density
- Spherical morphology
- Exceptional flowability
- Low oxygen
- Tailored PSD for specific printing methods
- Scalable volumes from lab to production
- 100 years of refractory metal experience
- Custom alloy development through R&D
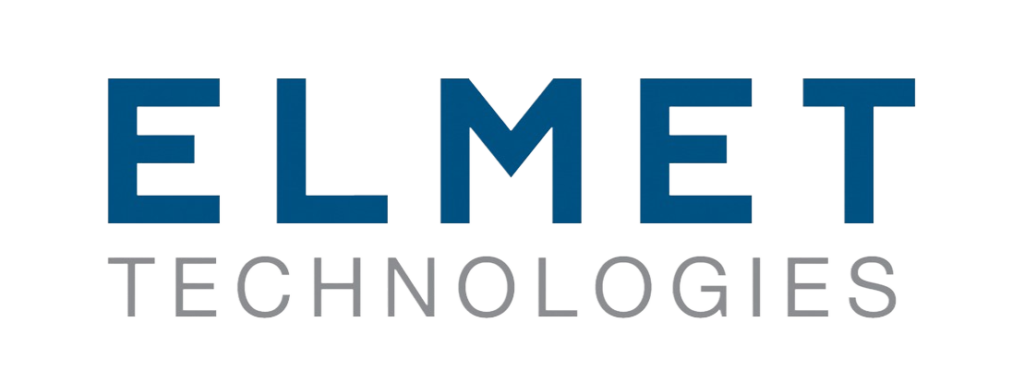
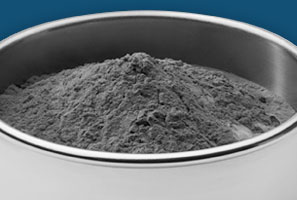
Materials and Specifications
Property | Unit | Nb | Mo | Ta | W |
Purity | % | > 99.95 | > 99.95 | > 99.95 | > 99.95 |
Mean Particle Size D50 | µm | 23 – 30 | 20 – 30 | 20 – 30 | 20 – 30 |
D10/D90 | µm | 10/40 | 10/40 | 10/40 | 10/40 |
Bulk Density | g/cc | 4 | 5 | 8 | 10 |
Hall Flow | s/50g | 14 – 16 | 8 – 10 | 5 – 9 | 5 – 8 |
Oxygen | ppm | 1500 | 400 | 300 | 250 |
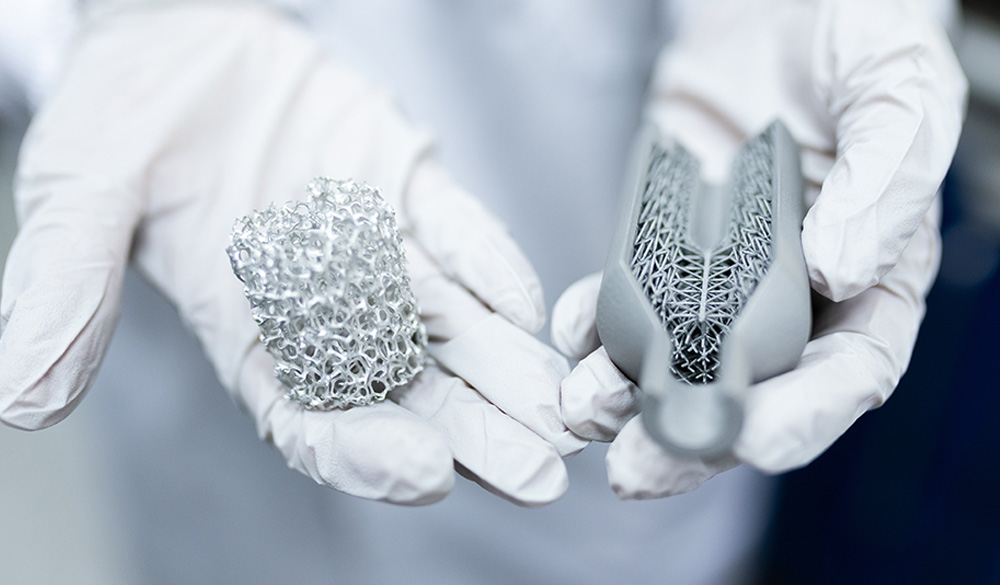
Advanced Refractory Metal Solutions
We are deeply committed to continuously expanding our portfolio while also exploring new and innovative applications for refractory metals. To support this, our vertical supply chain seamlessly begins with powder production and progresses through to a dimensionally accurate, post-processed printed part, ultimately ensuring readiness for the demanding needs of our customers.
Partner with Elmet Technologies for advanced additive manufacturing solutions in refractory metals, expertly designed to address the unique challenges of your industry.