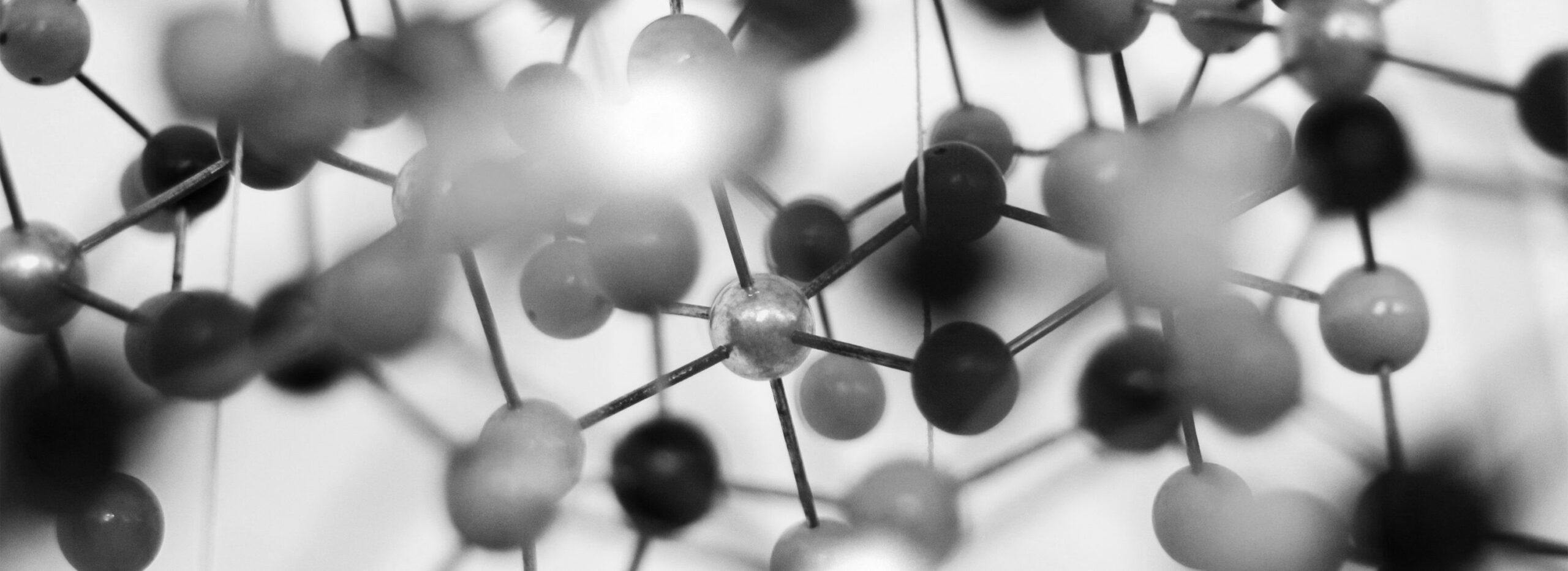
Alloy Devlopment
Elmet Technologies has a rich history spanning 100 years, where refractory metal alloy development has been fundamental to our success and growth. Our development of molybdenum alloys played a crucial role in advancing early space propulsion technologies. Additionally, our tungsten-heavy alloys have met the ever-increasing demands of modern medical and aerospace fields, providing essential properties for high-performance applications.
Additive Manufacturing has revolutionized both large- and small-scale production of alloy designs through techniques like direct energy deposition (DED) and laser – powder bed fusion (L-PBF). This innovation allows for quicker development and evaluation of new alloys, significantly reducing costs and lead times.
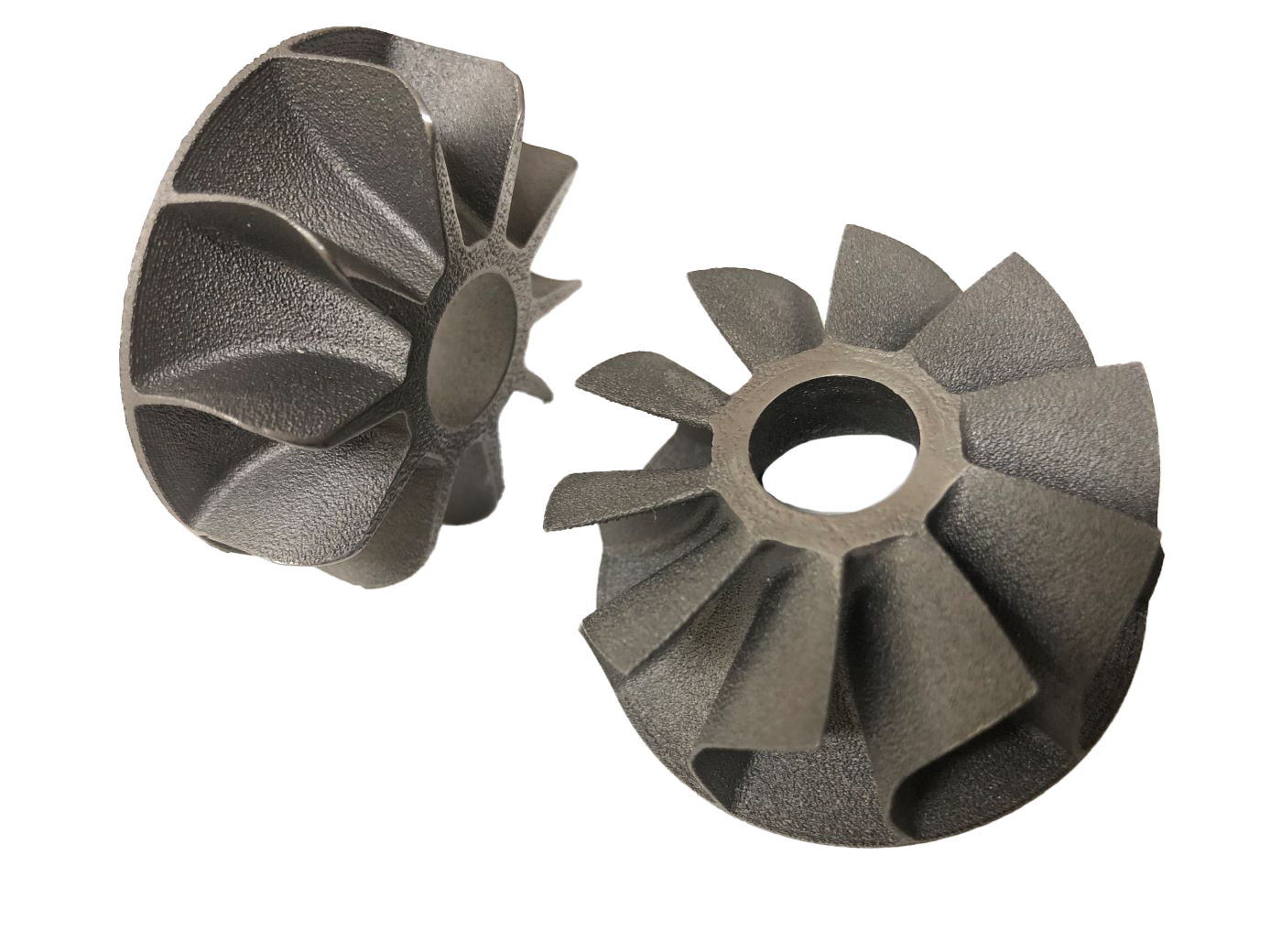
Laser – Powder Bed Fusion Development
Laser – Powder Bed Fusion (L-PBF): This technique commonly utilizes pre-alloyed powders to produce fully dense metal parts. By using powder mixtures, it streamlines the alloy development process, making it more time and cost-effective.
For more details on the laser – powder bed fusion process, check out the link below.
Alloy Development Through Additive Manufacturing
AM has transformed the way we approach new alloys for specialized applications. By leveraging AM processes, we can develop structure-property relationships among existing alloys. This enables the manufacture of high-value, complex components such as biomedical implants, aerospace parts, and defense components. These components require specialized manufacturing techniques and properties to meet industry standards.
The development of alloys in additive manufacturing has opened new avenues for innovation, driving advancements across various industries and ensuring that we continue to lead in providing advanced materials for a wide range of applications.
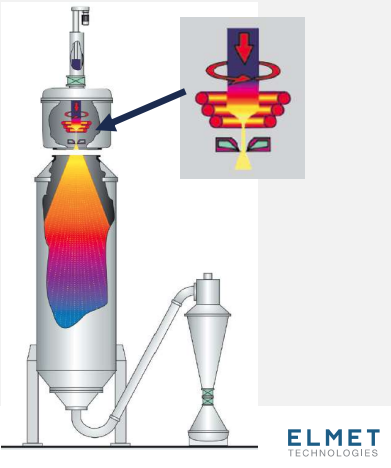
Laser- Powder Bed Fusion Alloy Devlopment
Directed energy deposition (DED) is an advanced additive manufacturing process that uses material in either powder or wire form. It utilizes a high-energy source to melt the material, which is then precisely deposited onto a component. DED offers exceptional versatility and precision, making it ideal for complex projects. It is renowned for repairing, enhancing, and coating larger metallic structures.
Laser-powder bed fusion (L-PBF) technology is our primary additive manufacturing method. However, upon request, DED is available to customers to meet diverse manufacturing needs.